I have visited several garment factories where I have closely worked with industrial engineers over my career span. I have met the owners of these factories. I am happy many are aware of these tools but many will end up losing scalability implementing and reaping the benefits of these basic tools.
From my discussions with a couple of other factory owners, I also observed that they also believe in the average cycle time of the sewing operations than the standard time established through software or using the Time Study method.
The reasons are usually subjective. In this article, I will walk you through why this statement is true.
Broadly speaking, the fashion cycle consists of three phases:
- Planning, design, and product development
- Sell-in;
- Production and delivery. The length of each phase varies widely from company to company. A phase can be as short as 12 weeks or as long as 30.
Below is the recent study details on fashion Cycle duration from McKinsey
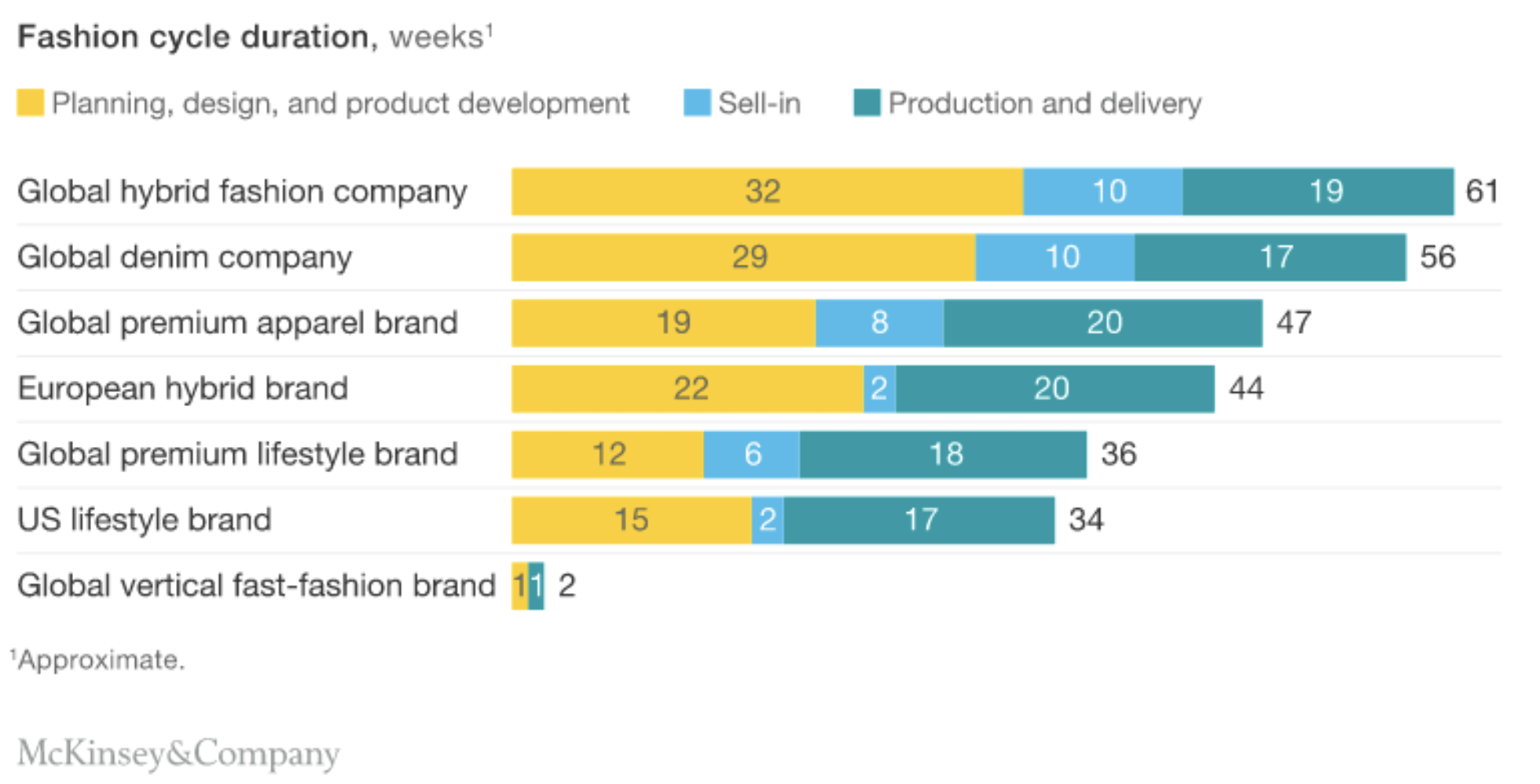
As the business type varies the greatest potential for compressing the calendar mostly tends towards production & Delivery. The manufacturers are often asked for improved efficiency, relook their line designs, improve handling time, use better techniques.
In simple words, we all are focusing on TIME.
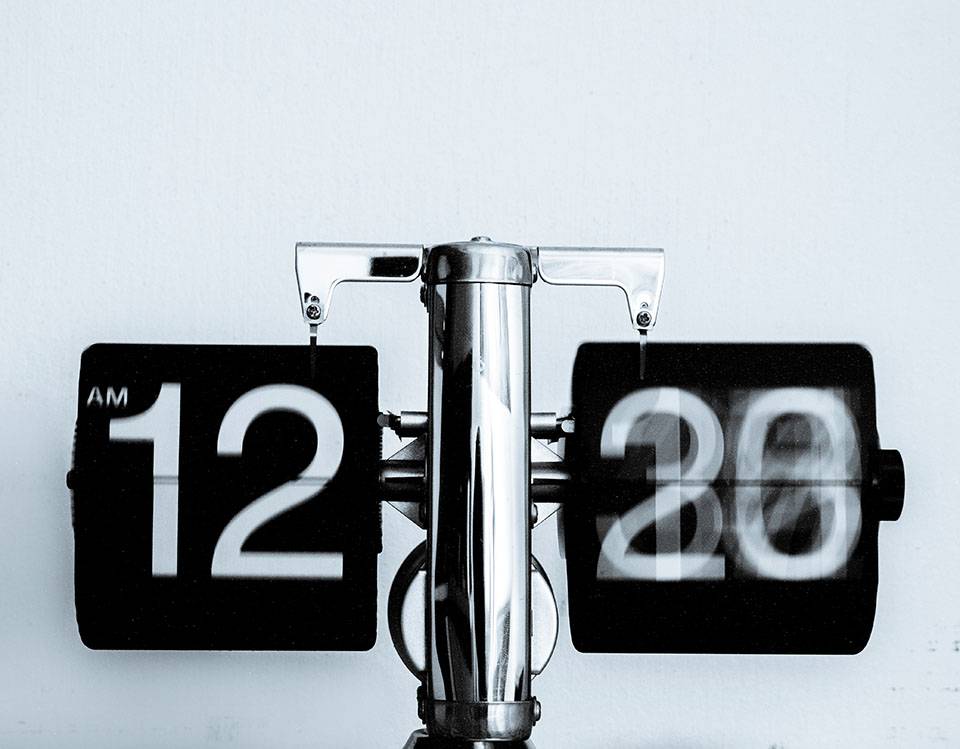
The standard working Time is 8hrs, which means 480 Min.
Every minute becomes crucial for any organization and how well we define and improve makes the difference between failure and success.
Time has become a key success measure in business. For example, in marketing, a product's success or failure often depends on "time-to-market," or how quickly a new product becomes available to the customer. We can define cycle time to Order Processing cycle time, finance perspective like cash-to-cash cycle time
Cycle time is the key to the competitiveness of a firm as it affects both price and delivery.
Here I would like to point out some myths that many practitioners tend to use to differentiate Cycle time / Lead time /Basic Time/Standard Time
Cycle time is usually defined as the time starting when the operation begins to the point of time when the operation ends.
Cycle time = Total Machine Time + Total Material handling time.
This leaves a question on what is Lead Time?
Lead time is defined as and when a request is initiated and ends with delivery.
Example Let’s say a customer orders a product on Jan 6. receives the order instantly and delivers the product on Jan 10th, yet work on the product begins Jan 8. Lead Time here is four days, while Cycle Time is two days.
Lead time is a latency between the initiation and execution of a process
At first glance, Cycle Time represents the effort in converting the order to delivery. It becomes the most favorable time for cutting it short.
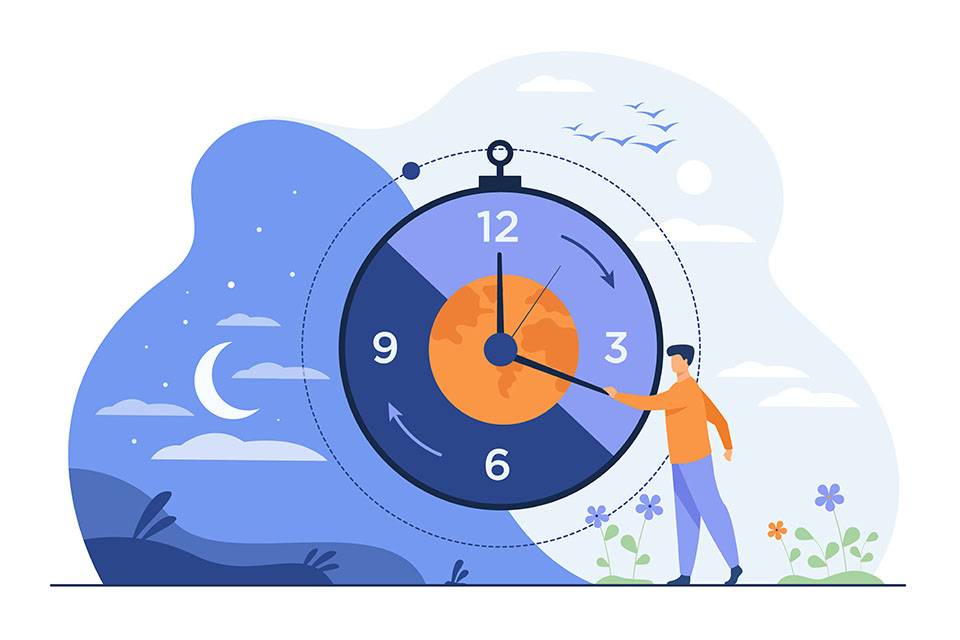
Basic Time
Basic Time is the time that is obtained by multiplying the rating factor to Cycle Time (Observed Time).
Basic Time = (Cycle Time × Performance Rating)/100
This Basic Time is also known as Normal Time. ** There are no Allowances added to Basic Time.
Standard Time
Practically nobody can do work continuously for a long time without taking a rest. During working there may occur machine and needle breakage as well as the need to manage bundle during working. Also, many other issues may occur during working.
These pre-defined failures or hindrances are called Allowances
Standard Time = Basic Time + Allowances
All the above definitions are well defined in all Industrial Books and Journals.
Practically, these cycle times can be standardized across all operations as most of the product lines are basic Shirts/Denim/Trousers/ T-shirts/Blazers. It's for the Manufacturer and Industrial engineer to analyze every cycle time and propose new methods of decreasing the timelines.
With turnaround time becoming a prime factor in attracting business, manufacturers must explore options to reduce the cycle lead-times.
As we advance from Cycle time we have MTM ( Method time Measurement). MTM is a Flexible, Multi-Level, Predetermined Time Standard that can be entered at any level to achieve the level of accuracy required by the user.
In the next article will see how these tools are implemented across business lines and how lean manufacturing gained momentum in every sector of manufacturing
RELATED TOPICS:#Apparel,Ajay Ravuri
Leave a comment
Our email address will not be published. Required fields are marked *
0 Comments