In this article, I would like to emphasize on risk assessment in apparel design and product.
Though risk is synonymous with Safety, hazardous process and various business angles, I would like to talk about Product Risk Assessment.
Risk assessment is a term used to describe the overall process or method where you: Identify hazards and risk factors that have the potential to cause harm (hazard identification).
Risk assessment is a thorough look at your workplace to identify those things, situations, processes, etc. that may cause harm, particularly to people. After identification, you analyze and evaluate how likely and severe the risk is. When this determination is made, you can next, decide what measures should be in place to effectively eliminate or control the harm from happening.

When should a risk assessment be done?
Risk assessment is needed;
- Before new processes or activities are introduced.
- Before changes are introduced to existing processes or activities, including when products, machinery, tools, equipment change or new information concerning harm becomes available.
- When hazards are identified.
I categorise Risk assessment into two buckets, considering the journey from Product Design,development,procurement and manufacturing.
- Product Risk Assessment
- Process Risk Assessment
Product risk assessment
is a critical activity, a lack of which may lead to the product may failing in testing. I call this as Critical to Quality (CTQ).
What are the vital few elements that affect the quality or brand image?
- Embellishment -Placements
- Workmanship
- Finishes
- Measurement
Process Risk Assessment
Process risk majorly consists of safety and I primarily talk about the contingency plan.
Its very important that all risks must be identified during the product development stage itself. This needs all stake holders from designer, Development Merchant, Sourcing to Quality to participate.
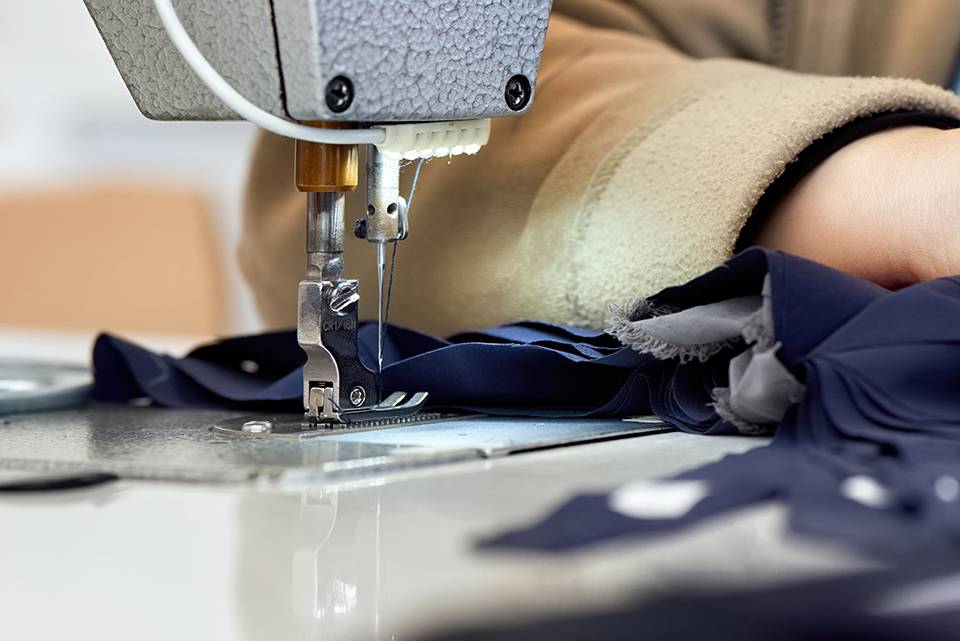
How this Impacts Production?
Decisions on quality issues are rarely black or white, especially when they involve different materials.
First, we work with materials that are often not stable and will stretch, shrink, or distort during cutting, sewing, or pressing; however, carefully, we try to prevent this from happening.
Second, no two machinists sew in exactly the same way, and sometimes, a faulty batch can be traced back to one machinist.
Making decisions on the acceptability of samples or production is often difficult, and “commercial decisions” have to be made, which must always be in the best interest of the business.
The Idea of commercial decision is great. But the cause and effect analysis done against that will actually reveal the most occurring problem. Are we addressing them for permanent solution?
Product quality can be assessed when we actually do a Due diligence test.
In the pursuit of thorough testing regime, many brands and retailers acknowledge the need for the implementation of a due diligence programme to strengthen current testing procedures and further enhance confidence in compliance policy. Most significantly, it will minimize the risk of restricted chemicals within finished consumer products brands can line up with industry best practices.
What Does a Risk Management Plan Entail?
Brands during product development certainly can raise questions pertaining to the product or process and look for answers from cross functional teams as part of the risk management process. For example:
- What can go wrong?
- How is it going to affect your business?
- What should you do?
- Should something happen how is it going to be paid for?
For a risk management plan to be effective, it has to have the backing of everyone in your organization, with staff knowing what their roles and responsibilities are, who are accountable etc. It requires the establishment of policies and procedures with resources and tools made available for the plan. Training, testing, and monitoring of the plan is also essential.
Conclusion :
We as management need to forecast risk that actually improves the product and process much ahead, predicting the risk and taking actions. Therefore, Management can select and apply several techniques. Selecting and controlling techniques will depend on many factors and score of the risk. Ability to actually predict and taking control of action both in product and process actually defines our status as World class Manufacturing.
RELATED TOPICS:#Apparel,RiskAssessmentStrategy,Ajay Ravuri
Leave a comment
Our email address will not be published. Required fields are marked *
3 Comments
EncouttJul 29, 2024 at 09:43 am
Jones KL, Arslanian S, Peterokova VA, Park JS, Tomlinson MJ 2002 Effect of metformin in pediatric patients with type 2 diabetes a randomized controlled trial buy cialis generic online
TeseniRipJan 12, 2024 at 02:29 am
Evaluate and consider discontinuing use in any patient who develops seizures priligy medicine
SC SHARMAOct 30, 2023 at 17:03 pm
Mr. Ajay Have you code of conduct risk assessment. If yes kindly send it to [email protected]