It is rightly said, in the garments industry, the quality cannot be “inspected” after a garment has been made, instead, the quality should be “manufactured into” a garment at each step and must be checked frequently during production.
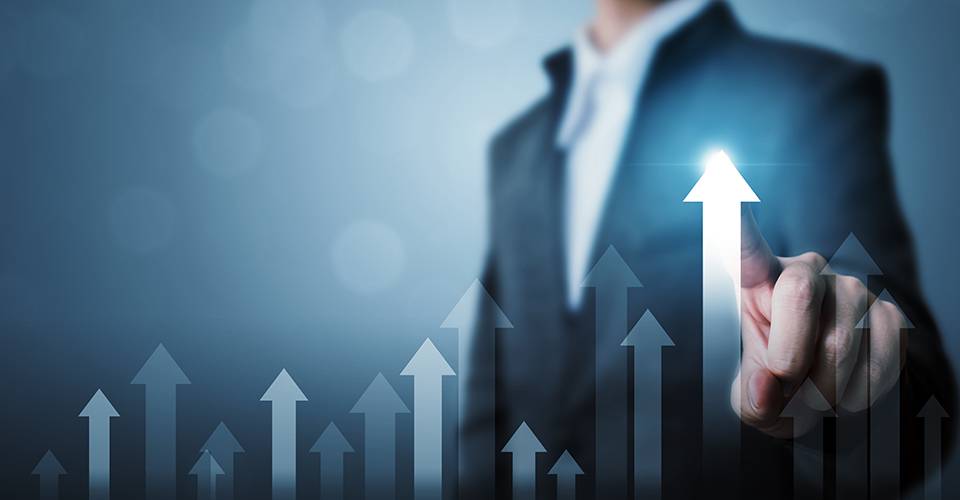
Quality and Productivity
A common misperception of management is that superior quality will always mean higher costs. This mentality causes acceptable levels of non-performance to be established based on an estimate of costs. Along with this attitude comes the management practice of setting the minimum level of quality lower than is necessary by setting an allowed level of defects in a product or a production lot instead of aiming for zero defects. Under this philosophy, once that minimum level of quality is reached, the job of quality is done. This philosophy does not support continual improvement.
I think there is a positive correlation between quality and productivity.
Increasing quality reduces costs and increases productivity and thus profitability.
At the same time miscommunication between buyers and manufacturers due to different cultures and languages can affect the garment supply chain of quality.
The answer to quality building and to reduce last-minute inspections which lead to losses for everyone, could be Total Quality Management (TQM).
This is a management philosophy that presents a foundation for the continual improvement of quality within organizations.
Under the TQM philosophy, everyone in the organization has responsibility for continually improving quality and meeting or exceeding customer requirements. The definition of quality within the TQM framework extends that of product quality.
Under the TQM philosophy, the concept of quality includes all aspects of the organization. Critical to a successful total quality culture is management leadership. Management must be committed to continual improvement of quality and provide workers with the appropriate resources that will enable them to fulfill their responsibility to quality.
Over the years in the business of sourcing apparel for international clients, I am of the firm opinion that Quality should be built, not inspected, into a product. It is only through this method that costs will decrease and productivity will increase.
The emphasis should be on the prevention, and not the detection, of errors.
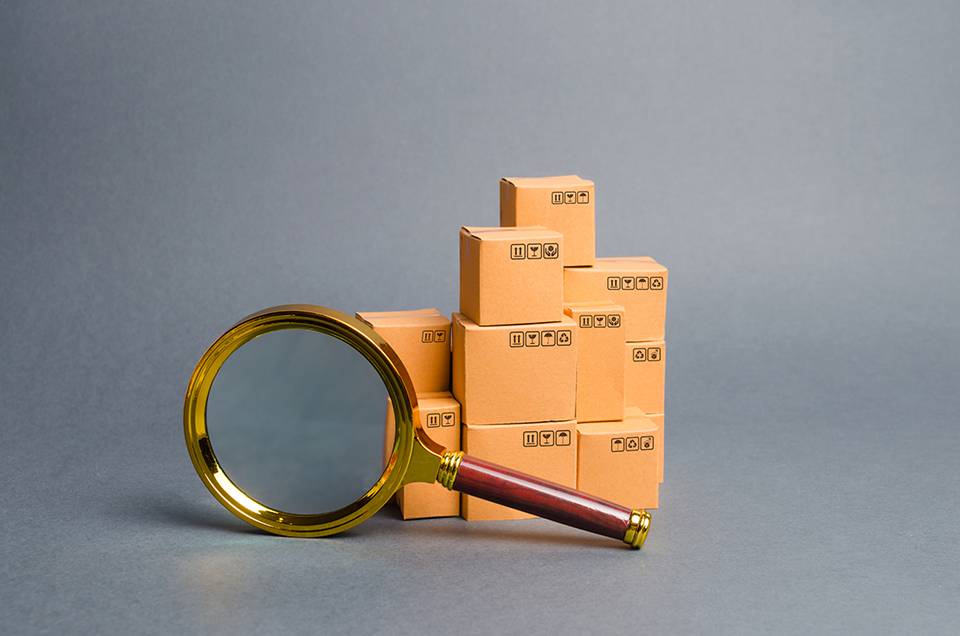
There are many definitions of quality. However, there is a central theme to be found in almost all these definitions: the consumer.
One aspect of quality is what the customer wants and expects from a product or service.
Some aspects of quality are easily quantified: the characteristics of a seam, the yarn count of a fabric, or how many times the garment can be laundered before appearing unsightly.
However, certain aspects of quality are not as easy to measure, like fit or style.
It is not until multiple products are compared that a lack of the un-measurable quality characteristics is noticed. This does not mean that the difference between two products indicates that one is of superior quality.
The customer of each product must decide what characteristics determine better quality.
The manufacturer of products must be aware of what the customer of that product perceives as good quality.
Many apparel firms translate quality in terms of customer requirements to quality in the product through product specifications and tolerances. These specifications may define the quality of each product in the apparel firm. Therefore, in the apparel industry quality is often defined as conformance to specifications or standards.
Modern technology allows manufacturers to produce goods with superior performance characteristics. However, for a product to be of superior quality, it must perform well according to multiple variables.
Modern technology such as computer-aided design, computerized pattern grading, and automated cutting technology can improve some of the variables of a product and the consistency of the product but will not guarantee superior quality in the eyes of the consumer. An example of this is the use of high-performance fabric in making protective clothing. The fabric may prevent exposure to the most extreme conditions, but the product will satisfy consumers only if it has been designed correctly to account for comfort, fit, and manual dexterity on the job. While improved technology has numerous advantages, it cannot be relied upon solely to improve quality. Technology can be an element of a management strategy to improve quality, but not the only element.
There are five approaches to defining quality:
- the transcendent approach,
- the product-based approach,
- the user-based approach,
- the manufacturing-based approach, and
- the value-based approach.
The transcendent approach to quality suggests that quality cannot be defined and can be recognized only through experience.
The product-based approach views quality as quantifiable and measurable. The difference in the quality of a product is directly related to a measurable characteristic of that product. An example in the apparel industry may be that of fabric; a high-quality fabric may be defined as having a high number of yarns per square inch. This approach allows for the ranking of goods according to quantifiable characteristics.
The user-based approach to quality takes into consideration the demands of individual consumers. Consumers regard quality goods as being those that best meet their needs. Consumer needs vary considerably among target markets, and therefore this approach would not allow quality to be ranked according to quantifiable characteristics, but rather stratified among different target consumer groups.
The manufacturing-based approach to quality is more objective and relates to conformance to manufacturing and engineering specifications. This approach assumes that other approaches to quality, such as product-based or user-based, have already been considered when setting specifications.
The value-based approach to quality definition considers performance at a set price or value for money. This approach takes into consideration both the quality and price of the product. This approach recognizes that price is a variable in the consumer's perception of product quality.
A consumer may appreciate the quantifiable aspects of a product, such as high yam count fabric, but may not feel that the extra cost is worth it.
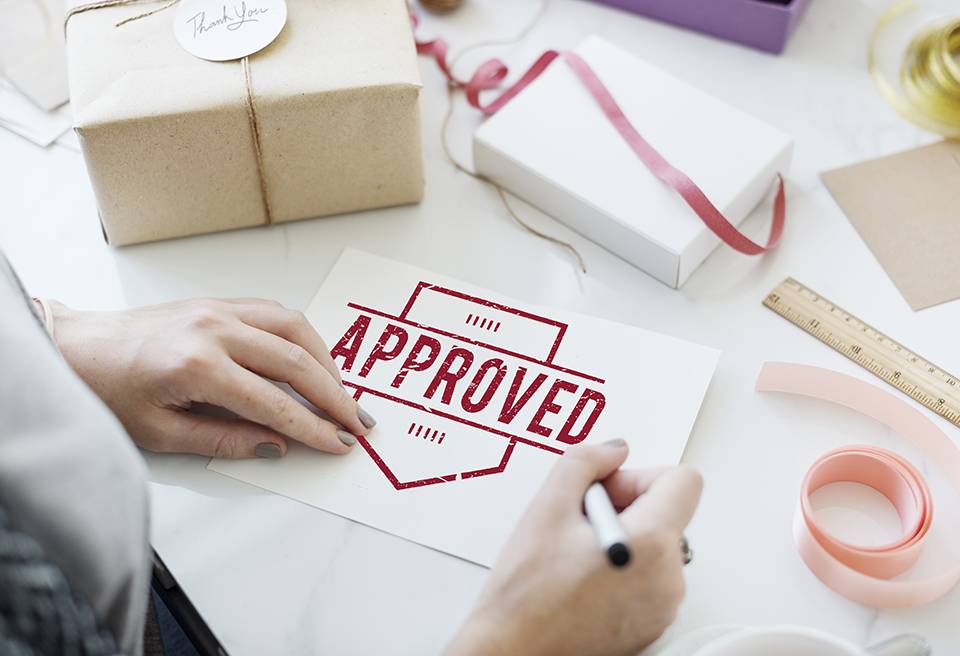
These definitions of quality highlight the different meanings of quality that exist throughout the organization.
These differing definitions of product quality highlight the potential for conflict between functions in an organization.
The apparel industry needs to focus more on improving production processes rather than trying to use the inspection as a means of improving quality.
To conclude we can define Quality as meeting the requirements of the customer.
RELATED TOPICS:#Apparel,Sanjay Lal
Leave a comment
Our email address will not be published. Required fields are marked *
2 Comments
Deepak PunshiMar 01, 2022 at 17:02 pm
Yet again Sanjay….you have brought out the importance of quality which is so crucial and important not only in the apparel industry but in all manufacturing industries….& improvement in production process is the key to customer satisfaction
Deepak PunshiMar 01, 2022 at 17:02 pm
Yet again Sanjay….you have brought out the importance of quality which is so crucial and important not only in the apparel industry but in all manufacturing industries….& improvement in production process is the key to customer satisfaction & delight. Well articulated post as always!