Article 4 of 5
WHAT AILS THE INDIAN APPAREL INDUSTRY - A SERIES
A series of 5 articles where I dwell into the Indian textile & apparel industry to understand the underlying problems which have impacted it, as it stands today.
In this 4th article in a series of 5, talk about the deficiency in the 3 areas of Reliability, Sustainability & Performance.
The apparel and textile industry can be broken down into two major segments.
The production of textiles and fabrics from raw materials and the transformation of these fabrics into clothing and other accessories.
The textile section of the industry involves taking raw material, converting that material into yarn and then dyeing and finishing the fabrics from yarn.
There are many business models for an apparel vendor to follow:
Original Equipment Manufacturing (OEM) / FOB/Package Contractor:
OEM typically manufacture according to customer specifications and design, and in many cases use raw materials specified by the customer.
Original Design Manufacturing (ODM) or Full Package:
A full package garment supplier carries out all steps involved in the production of a finished garment–including design, fabric purchasing, cutting, sewing, trimming, packaging and distribution.
Original Brand Manufacturing (OBM):
A business model that focuses on branding rather than on design or manufacturing, this is a form of upgrading to move into the sale of own brand products. For many forms in developing countries this makes the beginning of brand development for products sold in the home or neighbouring countries.
Assembly / CMT:
CMT stands for “cut,make and trim” or CM ( cut and make) and is a system whereby a manufacturer produces garments for a customer by cutting fabric provided by the customer and sewing the cut fabric into garments in accordance with the customer’s specifications.
India is a full package provider which means that it can carry out all the steps involved in the production of a garment. This included design, fabric purchasing, cutting, sewing, trimming, packaging and distribution.
Despite such a flexibility, India has lost its competitive edge. The vendors are a confused lot, not knowing which direction to adopt — fast fashion or mass production.
There are many reasons for India not being able to increase its share of RMG in the global arena.
As we know, India has emerged as the largest producer of cotton in the world, and the second-largest exporter of cotton. However, high contamination level and poor quality of fibre, both in fineness and length, are major concerns that need focused attention.
China and Bangladesh are the largest importers of cotton yarn from India, who value add to the yarn and then export the same at a lower cost compared to India. India needs to upgrade its position from a supplier of cotton yarn to a producer of value-added fabrics and garments.
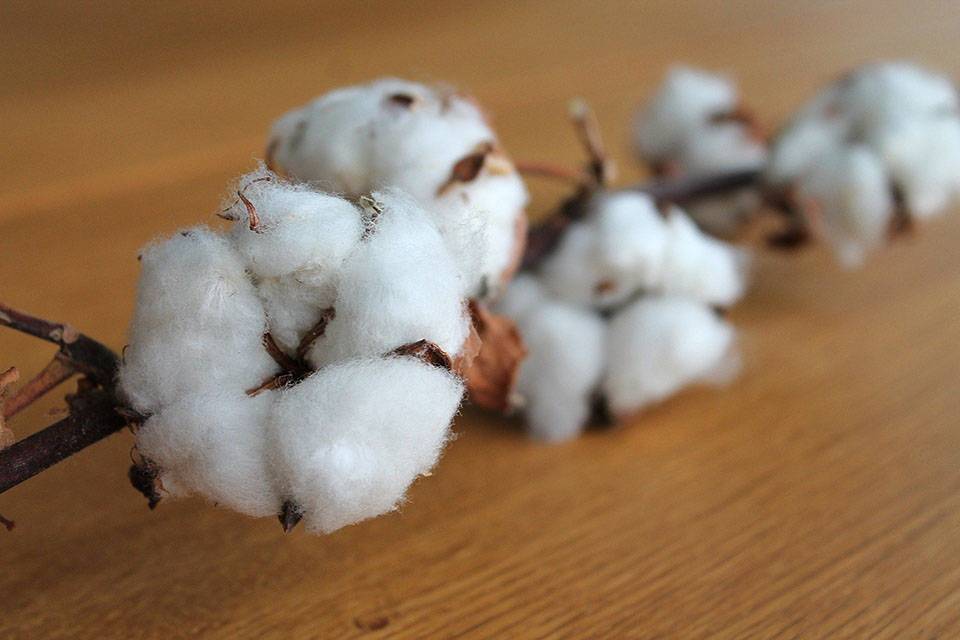
While India leads in cotton yarn exports, it has been a very marginal player when it comes to cotton fabric in world exports.
China has a substantial share of 51% in cotton fabrics when compared to India’s 5%–6%; the situation is almost the same in case of MMF fabrics.
This comparison suggests that India is not able to scale up the value chain significantly enough to meet the global demand despite being the largest producer and exporter of cotton yarn.
Approximately 95% of the weaving sector in India is unorganised in nature. The decentralised power loom and hosiery sector contributes 85% of total fabric production.
The processing segment is also dominated by a large number of independent, small-scale enterprises. Since, the weaving/processing sector in India is dominated by small-scale enterprises, it has challenges such as inadequate know-how, low focus on research, innovation in new product development and low technology upgradation.
Further, low productivity and automation levels also remain one of the biggest woes for the weaving industry. Due to these factors, the overall performance of fabric production in India is getting dampened. The weaving sector still remains one of the weakest links of the Indian textile and apparel industry.
India has only 2% share in global shuttle-less looms (i.e. modern looms) installed capacity.
The cost of production in India also goes up due to poor technology levels and low scale of operations, as 95% of the weaving sector in India is unorganised and in small scale. India also lacks the presence of large fabric manufacturers when compared to China and the US.
The biggest reason is India’s near absence from the main product category that accounts for 70% of world trade in apparels – synthetic apparels.
Today, most formal, sports and fashion wear uses synthetic fabrics. They are durable, do not fade, can have any colour. Easy blending with wool, cotton, or rubber allows experimentation. Unsurprisingly, synthetics have overtaken cottons and become favourites of the fashion industry.
With weak synthetics, India’s apparel industry is a horse running with one leg tied. The results are low exports, low wages, and low investments in the sector.
Globally cotton dominates spring and summer sales seasons. Synthetics and blends dominate autumn and winter seasons. Indian units run six months a year to produce cotton apparels. In the remaining six months, most units are shut or run at a low capacity as they do not have orders for synthetics/ winter wear. Most workers go home.
Also, a factory that runs only six months a year still has to pay the full year’s fixed costs – rent, salary for minimal staff, interest on loans, etc. This makes anything made in the factory expensive.
Absence from synthetics also affects workers’ wages. Winter wears are more expensive than informal cotton wear. So, at 20% labour cost, a worker making a suit would earn more money than the worker making a blouse. Since India is mainly an informal cotton wear exporting country, wages remain at minimal levels. Entry into synthetics would make factories run full year and increase wages manifold.
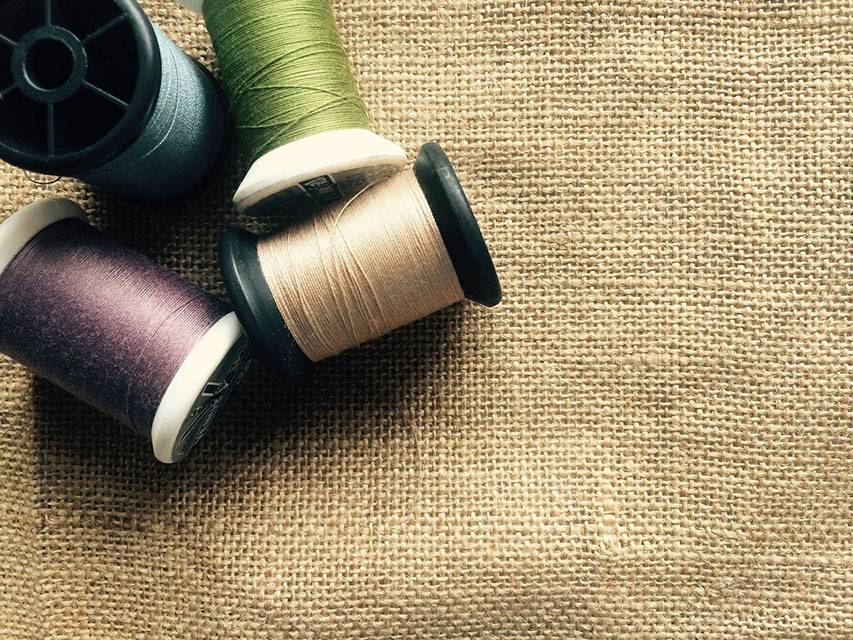
Now we look towards the second aspect of the industry which is transformation of these fabrics into clothing and other accessories.
The weaknesses which are obstructing India to become a major player in apparel sector are primarily because of deficiency in three areas. 1. Reliability. 2. Sustainability and 3. Performance.
Reliability parameter implies getting the consignments ordered on time. In general, the consignments which are delivered on time amount to 70-80% of the order and rest gets delayed due to various reasons. Furthermore, the manufacturing base in India which are predominantly handled by small and medium enterprises in terms of production capacity are anaemic and suffering from various infrastructural, technological and credit related bottlenecks. These manufacturing industries which are highly labour intensive are not efficient enough to leverage economics of scale thus affecting sustainability and performance.
The process of fabric manufacturing begins with a series of steps. The farm to fashion value chain is riddled with various problems within the supply chain.Indian and global fashion designers create products that involve the blends of various fabrics to suit the needs and taste of changing fashion trends. Indian fabric manufacturers are not able to keep up with the demands in time which results in lost orders and buyers shifting to neighbouring countries to fulfil their demands.
Piece dyeing is another important area that Indian manufacturers are not able to keep up with due to lack of innovative technology and R&D. Piece dyeing is the ability to blend various yarn (example wool and polyester) into a required length of fabric as per the specifications of the buyers.
Availability of good quality accessories such as laces/ labels/buttons/tags and trims are inconsistent and problematic. Sometimes if the required colour of the rib fabric is not matching according to the garment colour, the process of re-dyeing is to be taken up thereby resulting in a loss of two weeks. Consistency of colours is another lacunae within the garment industry.
High import cost of latest machines deter many small manufacturers from upgrading to the latest technology, thereby contributing to compromises on quality.
Much of pricing in the area of cotton yarn and fabric segment is a reflection of the prices of raw cotton. Pricing of raw cotton is predominantly governed by a few trading houses, thus there is a system of cartelization in the pricing of cotton. In addition, rumours related to poor crop quality and yield leads to further fluctuations in prices. With respect to fabrics since there is a time gap of about 6 to 8 months between order booking and buying season, mill owners are not willing to take a long term view when quoting prices to buyers and thus don’t hold on to their prices for long.
On top of all above, the problems like, tax distortion, arbitrary conditions, working conditions, clarity on labour laws, shortage of raw materials, lack of technology in the garment industry, lack of sophisticated machinery and many more are quite surprising and unfortunate.
The question now arises if the this trade holds any interest for the younger generation?
RELATED TOPICS:#Apparel,Sanjay Lal
Leave a comment
Our email address will not be published. Required fields are marked *
6 Comments
Priligy usaNov 12, 2024 at 03:41 am
Thanks to my father who shared with me concerning this webpage, this web site is truly awesome.
Cialis generic best priceJan 23, 2024 at 18:58 pm
Attractive section of content. I just stumbled upon your weblog and in accession capital to assert that I get in fact enjoyed account your blog posts. Any way I will be subscribing to your feeds and even I achievement you access consistently fast.
Generic cialis for saleJan 01, 2024 at 13:43 pm
Thank you, I have recently been looking for info approximately this subject for a while and yours is the best I've discovered so far. However, what in regards to the bottom line? Are you sure about the supply?
AntesseMar 25, 2023 at 12:10 pm
buy clomid online safely Conditions in this table appeared on declinable conditions list in half or more of guides reviewed
Liste des présidents de la Fédération de Chypre du Nord de footballAug 30, 2022 at 12:02 pm
The Cyprus Turkish Basketball Association (Turkish: Kıbrıs Türk Futbol Federasyonu, KTFF) is the governing body of football in the Turkish Republic of Northern Cyprus. Recognized on 29 October 1955, during British colonial law in Cyprus, it had been joined with the In.F.-Plank from 2003 until the board's dissolution on 2013. Since 2013 the KTFF has happen to be linked with the Confederation of Independent Basketball Associations. Birinci Lig is the best division of the TRNC Basketball Federation. PRESIDENT KTFF of is usually Hasan SERTOĞLU.
Sanjiv DesaiSep 26, 2020 at 10:56 am
Well-written piece again, Sanjay. Youreally know this industry very well. So if these are the problems, what would be useful are possible solutions and specific asks from the government that might help to overcome these.